公路工程施工方案
手機:M版 分類:計劃方案 編輯:小景
公路工程施工方案 標籤:電子工程師
4.2、路面工程
施工前,嚴格對下承層進行檢查,在符合規定標高和壓實強度的路基上進行路面底基層、基層的施工。施工前選擇一段長度為100~200m的路段進行各結構層的鋪築試驗,以檢驗擬定的施工工藝流程和施工方法的合理性、施工組織及施工機械的適應性。通過修築試驗段,優化拌和、運輸、攤鋪、碾壓等施工機械設備的組合及各工序的銜接,明確各施工人員的崗位職責,提出混合料生產配合比,提出施工標準和方法。
4.2.1、級配碎石底基層施工
(1)、配料準確,混合料必須均勻,沒有粗細顆粒離析的現象。
(2)、在最佳含水量時,壓實度(按重型擊實標準控制)不小於96%。
(3)、級配碎石所用石料的壓碎值不大於35%。
4.2.2灰土底基層施工
(1)下承層準備與測量放樣
施工前對下承層按質量驗收標準進行驗收,並精心加工。之後,恢復中線。
(2)備料和混合料拌和
使用的原材料符合質量要求,使用挖掘機集中進行拌和。
(3)混合料攤鋪
採用推土機及刮平機按試驗路段所求得的松鋪係數進行攤鋪。
(4)整平碾壓
混合料攤鋪、整型后,按技規所定壓實方法進行壓實,在平曲線段,壓路機由內側向外側碾壓。路面兩側,多碾壓2-3遍。在碾壓過程中,如有“彈簧”、鬆散、起皮等現象,要及時翻開重新拌和,或用其它方法處理,使其達到質量要求。
(5)洒水養生
洒水養生時間不少於7天,未鋪基層時,除洒水養生車輛外,禁止其他車輛通行。
4.2.3二灰碎石底基層施工
(1)、準備下承層
底基層施工前,對下承層(填方路基)按規範要求的質量標準檢查驗收,並經監理工程師批准。使下承層表面平整、堅實,具有規定的路拱,沒有任何鬆散材料和軟弱地點。
(2)、施工放樣
在下承層上恢復中線,直線段每15~20m設一樁,平曲線段10~15m設一樁,並在兩側路肩邊緣外設指示樁,進行水平測量,在兩側指示樁上用明顯標記標出石灰土底基層邊緣的設計標高。
(3)、拌和集料
集料中超尺寸顆粒予以篩除。生石灰在使用前7~10天進行充分消解。拌合採用500噸/小時的強制式粒料拌合機拌合,用8噸自卸車裝運。
拌合時將礫石、石灰和粉煤灰按重量比裝入拌合機,在略大於最佳含水量的情況下拌合均勻。拌合合格的混合料及時用自卸車運抵攤鋪現場。
拌合時,拌合的時間和用料稱量應準確,加水應準確,應視運輸的遠近和天氣情況,在徵得監理工程師的同意后,調整加水量,以保證混合料在壓實前達到最佳含水量。
(4)、攤鋪集料
根據試驗段確定的松鋪係數,用攤鋪機將集料均勻地攤鋪在預定的寬度上,表面力求平整,並有規定路拱。攤鋪過程中,應將土塊、超尺寸顆粒及其他雜物揀除。除洒水車外,嚴禁其它車輛在集料層上通行。
(5)、碾壓
整形后,當混合料處於最佳含水量±1%時,進行碾壓。用振動壓路機在路基全寬內進行碾壓。直線段,由兩側路肩向路中心碾壓;平曲線段,由內側路肩向外側路肩進行碾壓。碾壓時,後輪應重疊1/2輪寬;後輪必須超過兩段的接縫處,後輪壓完路面全寬時,即為一遍。碾壓一直進行到要求的密實度為止;同時表面無明顯輪跡,一般需6~7遍。壓路機的碾壓速度,頭兩遍採用1.5~1.7km/h,以後採用2.0~2.5km/h。嚴禁壓路機在已完成的或正在碾壓的路段上“調頭”和急剎車,以保證穩定土層表面不受破壞。
(6)、接縫和“調頭”處的處理
兩工作段的搭接部分,採用對接形式。前一段拌和后,留5~8m不進行碾壓;后一段施工時,前段留下未壓部分,一起再進行拌和。拌和機械及其他機械如必須在上“調頭”時,採取覆蓋10cm厚砂礫的辦法,保護“調頭”部分表層不受破壞。
(7)、養生
二灰碎石底基層在養生期間應保持一定的濕度,不應過濕或忽干忽濕。養生期一般不少於7天。採取洒水養生的方法,每次洒水后,用兩輪壓路機將表層壓實。養生期間除洒水車外,其它車輛一律禁止通行。
4.2.4、水泥穩定碎石(礫石)基層施工
該工程的水泥穩定碎石厚度為20cm。
4.2.4.1、測量放樣
(1)、在底基層頂面恢復路中線。直線段每15~20m設一樁,平曲線段每10~15m設一樁,並在兩側路肩邊緣外設標示樁。
(2)、在兩側標示樁上用明顯標記標出水泥穩定基層邊緣的設計標高,以保證攤鋪質量。
4.2.4.2、準備下承層
水泥穩定基層的下承層(二灰碎石)表面應平整、堅實,具有規定的路拱,沒有任何鬆散的材料和軟弱地點。下承層的平整度和壓實度應符合設計標準。過路管道回填部位要按照相應結構層要求施工,並與原結構層相接密實無錯台。在攤鋪基層前將底基層表面洒水潤濕,但不能存有積水。
4.2.4.3、廠拌法施工
(1)、本工程採用廠拌法生產水泥穩定混合料的方式,拌合採用500噸/小時的強制式粒料拌合機拌合,用8噸自卸車裝運。
(2)、廠拌法全路段施工前,應進行實驗段的施工。一方面檢驗工程的材料、配合比、拌合機械、攤鋪機械、壓路機械和施工工藝;另一方面是確定現場攤鋪時虛鋪厚度,確定松鋪係數,保證壓實厚度和密實度,同時總結出最佳碾壓程序。實驗段完成後,進行施工總結,將總結報告上報監理工程師批複,合格后開始全路段攤鋪。
(3)、拌合時先將水泥、碎石(礫石)按重量比裝入拌合機,在略大於最佳含水量的情況下拌合均勻。拌合合格的混合料及時用自卸車運抵攤鋪現場。拌合時,拌合的時間和用料稱量應準確,加水應準確,應視運輸的遠近和天氣情況,在徵得監理工程師的同意后,調整加水量,以保證混合料在壓實前達到最佳含水量。
(4)、測量人員在開始攤鋪前,應按設計標高釘好鋼釺,並掛好基準線。
攤鋪採用攤鋪機完成。控制好攤鋪機的運行速度。首先經過試驗段施工,確定水泥穩定碎石(礫石)基層的最佳松鋪係數、最佳碾壓程序,用以指導大面積施工。攤鋪過程中如有離析現象設專人點補,以確保攤鋪面的均勻平整,沿縱向每隔10m為一斷面檢測攤鋪后的頂面高程,發現問題及時調整。
(5)、碾壓時應特別注意混合料的含水量,並按市政道路路面基層施工技術規範中的操作規程進行。碾壓時間控制在水穩基層初凝以前,一般不超過兩小時。碾壓工作用振動壓路機和輪胎壓路機完成,自路邊向路中碾壓錯1/2輪,膠輪壓路機錯一輪胎寬度。先用振動壓路機不掛振碾壓一遍,再掛振一擋碾壓至密實度達到技術規範標準,最後使用膠輪壓路機消除表面輪跡。
(6)、壓實面應無錯台、鼓包、坑凹、裂縫和鬆散情況,不合格的部位應進行整改。碾壓時應注意嚴禁在完成的或正在碾壓的路段上調頭和急剎車,碾壓成型后禁止一切車輛通行。
4.2.4.4、養生
(1)、成品表面洒水養生,保持7天表面濕潤。如遇炎熱天氣,來不及洒水時,可使用彩條布覆蓋成品表面。
(2)、養生期間禁止車輛通行,並派專人進行交通管制。
(3)、養生期結束,應按設計要求立即噴洒瀝青封油層。
4.2.4.5、檢驗與驗收
對已完成的水泥穩定基層在自檢合格的基礎上報監理工程師抽檢,合格後方可進行下一步工序施工。
4.2.5、瀝青混凝土路面面層施工
本工程路面面層做法為:0.5cm封油層+5cmAC-25瀝青砼(方孔篩)+4cmAC-16瀝青砼(普通瀝青)。
4.2.5.1、噴洒封油層
水穩基層施工完畢,報監理工程師檢驗合格後進行封油層施工。封油層用瀝青灑布機進行噴洒,要求噴洒均勻,無空白現象發生。每平方米噴洒用量0.8~1.2千克。
4.2.5.2、普通瀝青混合料拌和各種規格冷骨料由五格冷料倉通過調速電機控制的小皮帶放料到主皮帶上,完成骨料的粗配,主皮帶把粗配料送入滾筒,通過燃燒器對骨料加熱,由熱電偶監測料溫,自動調節燃燒器的風油比,使骨料溫度達到設定值。熱料經提升機進入振動篩,把熱料按目標配合比的規格要求分篩到不同的熱料倉(篩網尺寸可根據要求更換),由計算機控制各熱料倉拉門,按輸入的生產配合比自動配料、計量,然後放料到攪拌鍋進行攪拌,同時添加經計算機配比控制計量的石粉及瀝青,拌和40秒后,完成成品料的生產。
4.2.5.3、運輸
材料運輸至現場應注意以下問題:
⑴、來料的溫度一定要滿足攤鋪溫度,即不低於110℃~130℃,不超過160℃為宜,為此在現場應有質量人員對油溫進行測定。
⑵、車輛等候時,相互之間應有一定的距離,倒車、停車、卸載應設專人指揮,防止運輸車輛與攤鋪機發生碰撞影響攤鋪質量。
⑶、自卸車卸料后應將負載卸凈,並聽從指揮離開,避免粒料倒在攤鋪機受料斗外影響攤鋪工作正常進行。
4.2.5.4、攤鋪
⑴、高程控制:施工中除底面層掛金屬線以外,中、表面層採用浮動基準梁控制平整度和厚度的施工方法。
⑵、瀝青混合料必須緩慢、均勻、連續不間斷地攤鋪,攤鋪過程中不得隨意變換速度或中途停頓,攤鋪速度應根據拌合機產量,施工機械配套情況及攤鋪層厚度、寬度確定,下面層為2米/分鐘,中表面層為3米/分鐘。
在攤鋪過程中,攤鋪機螺旋送料器應不停頓的轉動,兩側應保持有不少於送料器高度2/3的混合料,_並保證在攤鋪機全寬度段面上不發生離析,在熨平板按所需厚度固定后不得隨意調整。
⑶、本工程使用TITAN423瀝青攤鋪機完成瀝青砼的攤鋪工作,用機械攤鋪混合料時,不應用人工反覆修整。
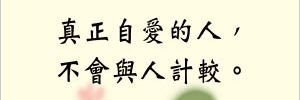

相關範文
- ·道路工程施工方案
- ·公路工程施工監理合同範本條文說明
- ·公路工程施工監理合同通用條件
- ·公路工程施工監理合同附件
- ·公路工程施工監理合同協議書
- ·道路工程施工合同
- ·工程施工方案
- ·模板工程施工方案
- ·管道工程施工方案
- ·防水工程施工方案
- ·弱電工程施工方案
- ·清淤工程施工方案
- ·排水工程施工方案
- ·安裝工程施工方案
- ·安全隱患排查工程施工方案
- ·裝飾裝修工程施工方案
- ·農村公路建設項目工程施工合同
- ·工程建設招標投標合同(土地工程施工監
- ·工程建設招標投標合同(土地工程施工監
- ·工程建設招標投標合同(土地工程施工監
- ·公路工程承包合同
- ·公路工程質檢部職責
- ·公路工程開工典禮主持詞
- ·建築工程施工突發事故應急演練方案
- ·建設工程施工合同(港口1)
- ·建設工程施工合同
- ·小區綠化工程施工合同
- ·建築裝飾工程施工合同
- ·水利工程施工合同
- ·建築裝飾工程施工合同(2)
- ·建設工程施工合同(電力2)