關於安全生產的文章
手機:M版 分類:工作體會 編輯:得得9
關於安全生產的文章 標籤:安全知識
關於安全生產的文章
“寧願聽到罵聲,不願聽到哭聲”----淺析自己對安全生產管理的認識
作為一名安全管理人員,我很喜歡安全格言,如果遇到新鮮的就要記下來,比如“嚴是愛,松是害,疏忽大意事故來。嚴是愛,松是害,保障安全利三代。”這些安全順口溜,之所以能夠流傳,是因為說的都是大實話。
“嚴是愛,松是害”,說得非常有道理,但有道理,未必人人能接受。嚴格管理,管理行為很嚴厲,避免了事故,也可能會招來反對埋怨牢騷甚至是咒罵;松是害,管理鬆鬆垮垮,領導不敢得罪人,沒出事故“你好我好大家好”,出了事故造成傷亡,受害者流血又流淚,被處罰人也會受到很大的挫折。所以,還有一句大家耳熟能詳的話:“寧願聽罵聲,不願聽哭聲。”這哭聲和罵聲裡面有學問,往深里說:哭聲和罵聲密切關聯,互為前提。有罵聲可能就沒哭聲。如果管理不嚴格,沒有罵聲,出了事故哭過之後,還會有更大的埋怨。對哭聲和罵聲的關係,有不少人整天研究,就是沒人公布研究成果。曾經有人說過忽視安全生產就是對職工犯罪。對安全要嚴加管理,要明知山有虎,偏向虎山行。寧聽罵聲,不聽哭聲。安全生產都表現在具體小事上。大事故都是有小違章引起的,沒發生事故前的事是小事,發生了就是大事。要堅決從小事抓,抓小事,成大事;抓小事,防大事。找事的目的是為了不出事。違章不一定出事,但出事肯定是違章。對習慣性違章,不能習慣性不管。人們的每次違章並不肯定導致事故發生,100次違章可能也不會發生一次事故,但也可能一次違章你就連感到遺憾的機會都沒有了。你能把握違章發生事故的隨機性嗎?答案是肯定的:不能。你願意將自己的安全建立在“幸運”的基礎上嗎?肯定不會!說到底最最關鍵的還是控制不安全的行為及潛在的危險,靠大家的安全意識和安全責任。
罵聲中委屈的是安全管理人員;哭聲中受傷害的是員工。無論是哭聲,還是罵聲,我相信不會有人願意去聽。心情本來好好的,突然挨頓罵,那感覺可遠遠超過一盆髒水潑在身上;凈聽到些哭聲,也不會好受到哪兒去。“寧願聽到罵聲,不願聽到哭聲”,只是在二難條件下的一種無奈選擇。
安全生產領域有一個十分重要的“海因里希”事故法則,是美國著名安全工程師海因里希提出的300∶29∶1法則。這個法則意思是說,當一個企業有300個隱患或違章,必然要發生29起輕傷或故障,在這29起輕傷事故或故障當中,必然包含有一起重傷、死亡或重大事故。這一法則用於企業的安全管理上,即在一件重大的事故背後必有29件“輕度”的事故,還有300件潛在的隱患。
了解“海因里希法則”的目的,是通過對事故成因的分析,讓人們少走彎路,把事故消滅在萌芽狀態。
如果我們把“海因里希”的300:29:1安全法則,從另一個角度去理解就能更好做好安全生產了。即培養一個良好習慣,必須經過29次重大改進或糾正,每次改進和糾正就要做300次的重複動作。也就是說,為了培養員工良好的安全習慣,需要進行多次反覆的改進和完善,而每一次改進和完善之後,又要經過無數重複動作和嚴格認真地落實,最終達到實現員工養成一個良好習慣的目的。從以上的要求中,我們不難發現要培養員工的良好習慣,不是一件容易的事情,要經過艱苦的努力才能成功。
在日常的安全管理過程中管理人員要勇於做“黑臉包公”,要從查找人的不安全行為抓起,不搞下不為例。美國著名的杜邦公司曾經作過事故統計,安全生產事故歸根到底96%是由人的不安全行為造成的。心理學上有個“破窗效應”。美國斯坦福大學心理學家菲利普·辛巴杜找來兩輛一模一樣的汽車,分別把他們放置在中產階級社區和雜亂街區。他把停在中產階級社區的那輛車的車牌摘掉,頂棚打了個洞。結果這輛車一天之內就被人偷走了。而放在雜亂街區的那輛車擺了一個星期卻仍舊完好無損。而把這輛車也打了一個洞,結果僅過幾個小時這輛車也被偷走了。如果有人打壞一棟樓的窗玻璃卻不被制止,受這塊玻璃的暗示,可能就有人去打破更多的玻璃。
作為一名安全管理人員千萬不能做過頭,為了聽罵聲而聽罵聲;不要成為偏執狂,就是要聽罵聲,愛聽罵聲。這就走向了安全管理的反面。有的媒體的褒獎宣傳,塑造了讓人難以接受的安全管理者形象。我們把這個宣傳的形象描繪下來,是什麼樣的呢?“鐵青的面孔,鐵石的心腸,鐵打的手腕”,說話擲地有聲,吐口吐沫都能把地板砸幾瓣兒。這簡直就是不食人間煙火的機器人。如果這樣的機器人是最好的安全管理者,那我們這些人做的工作,還不如交給機器去做。人和其他動物的區別是人具有主觀能動性,具有獨立的思維方式,安全管理者不能是機器人。為了不聽到哭聲,寧可聽罵聲,前提是同情心,是責任感,是人的感情存在,是人性化的一種表現。如果管理者沒有人性,沒有臉皮,沒有自尊心,任什麼人罵都不怕,反而有意去找罵,這實際上變現出一種不好的管理心態。我們在安全管理上見到最多的是批評、嚴肅批評甚至是勃然大怒。依我看,只要管理者主觀上沒有惡意,作為員工都應該接受。“聽得進批評,才沒有哭聲”。
“嚴是愛,松是害”,嚴格是為了員工不受傷害,是為了員工自己好。員工應該理解嚴格管理的出發點。如果別人為他好,他還要罵別人,那實在是不知好歹了,是素質問題。管理上按制度去辦,無論什麼崗位,無論什麼身份,安全面前,安全管理面前,安全管理制度面前,一視同仁。受到處罰,員工有什麼理由去罵管理者?要罵只能罵制度,而制度不是針對員工每一個人制定的,罵制度也毫無道理可言。
當然,安全管理沒有哭聲沒有罵聲,只是理想境界。沒有哭聲,是我們追求的結果;沒有罵聲,很多情況下不太可能。因為,人們的利益不同,思想認識不同,修養水平不同,受到處罰的反映也不同。但是,我們在管理中可以做到的是公平,“一碗水端平”,任何人沒有話說。管理要人性化,尊重他人尊重自己,讓被管理者知道管理者的良苦用心,才能達到“沒有罵聲也沒有哭聲”的安全管理理想局面。
“Would rather hear the quarrelling sound, unwilling to hear the cry sound” ------on my own understanding of the management of production safety
As a safety professional, I am very like safety aphorism, if encounter fresh going down, such as" strict is the love, the pine is the evil, careless accident. Strict is the love, the pine is the evil, protect safety benefit three generation." This safety patter can be spread, because said is the truth.
“Strict is the love, the pine is the evil," said very reasonable, but justified, not everyone can accept. Strict management, management is very strict, avoids the incident/accident, may also be brought against complain even cursing; pine is the evil, management slack, leading dare not offend a person, not an accident" good position everyone I am ", the accident casualties, victims of bloodshed and tears, the person being punished will be greatly frustration. Therefore, there are a people for having heard it many times as saying: “would rather hear the quarrelling sound, unwilling to hear the cry sound." The cries and condemning the inside knowledge, deep said: crying and condemning the closely related, each premise. A favor may not cry. If the management is not strict, not condemning, accident after crying, there will be a greater blame. To cry and condemning the relationship, there are many people who study, is not being published research results. Someone once said that ignores safe production is the worker crime. On the safety management to strictly, to knowing that mountain tiger, toward danger. Listen to voices, do not cry. Safety production performance in specific matters. Big ancient capital is a small violation caused by the accident never happened before, it is trivial, produced is important. To resolutely from small catch, catch thing, event; grasping things, and events. The purpose is to find not to have an accident. Violation is not must have an accident, but the incident is certainly illegal. On habitual violation, cannot be used no matter. People are not sure every violation cause accident occurs, the 100 violation may not be an accident, but may also be a violation you even have no chance to regret. Can you hold violation accidents randomness The answer is yes: not. Would you like build your safety base on the "lucky” Certainly not! In the final analysis, the most critical is to control the unsafe behavior and potential risk; we rely on the sense of safety and safety responsibility.
Favor of grievance is safety management personnel; the crying of hurt is the employee. Whether it is crying or swear, I don”t believe there are people willing to listen. The mood was good, suddenly and scolding, that feeling can be much more than a basin of the slops in the body; hear the cry of the net, not by where to go. “Would rather hear the quarrelling sound, unwilling to hear the cry", but in two difficult under the conditions of a helpless choice.
Safety production areas have a very important" Heinrich accident principle” is a famous American Safety Engineer Heinrich proposed 300: 29: 1. This principle means that, when a company has 300 hidden or violate the rules and regulations cases, must have 29 minor injuries or fault, in the 29 minor accident or fault, must contain one serious injury, death or serious accident. The rule for the safety management of enterprise, i.e. in a major accident must be behind 29 piece" mild" accident, there are 300 potential pitfalls. Understanding of "Heinrich principle ", is based on the cause of the accident analysis, let people take less roundabout way, the accident nipped in the bud.
If we put the “Heinrich principle” of 300: 29: 1 safety rules, from another perspective to understand better the safe production. Is to cultivate a good habit, must go through 29 major improvements or corrected each improvement and correction to do 300 times to repeat the action. That is to say, in order to train staff of good safety habits, needs to be repeated many times to improve and perfect, and every time to improve and perfect, and after numerous repetitions and scrupulously fulfill, finally achieves realizes the employee to develop a good habit .
From the above requirements, we discover not hard to nurture good habits, not an easy thing to do, to go through the hard efforts to succeed. In the daily safety management process .the professional should dare to do" black-faced ", from look unsafe behavior to grab, do not to be taken as a precedent. The famous American company DuPont once accident statistics, production safety accident in the final analysis 96% is caused by people”s unsafe behavior. Psychology has a" broken window effect". The United States Stanford University psychologistPhilip Zimbardofind two cars as like as two peas car, respectively, setting them in the middle class community and mixed and disorderly block. He parked in a middle-class neighborhood of the car that took off, ceiling hole. Results the car was stolen only one day. Put in mixed and disorderly block that car still intact before a week. But the car also hit a hole, only a few hours of this car was stolen. If someone broke a building window glasses is not prohibited by the glass, hint, and might have to break more glass.
As a safety professional do not overdo it, in order to listen to and hear voices cursing; not to be paranoid, it is listen to the voices, to hear voices. It was against gone to the safety management. Some media praise for publicity, create unacceptable safety managers image. We put the publicity image depicting down, what is it “Livid face, heart of stone, iron wrist", speaks extremely elegant and valuable, spat can give the floor a few petals. This is simply as the robot behavior. If the robot is the best safety managers, that those of us who do the work, rather than to the machines to do. The difference between human beings and animals is that people have the initiative, independent thinking, safety management is not robot. In order not to hear the cry, would rather listen to voices, the premise is compassion, responsibility, is the people”s feeling, it is a manifestation of human nature. If managers are not human, no face, no pride, what people call are not afraid, but intends to call, which actually show a good management mentality.
Here give an example of city management: as some city management officers, found business stall hawker, like "mopping up" see things move then penalty, see some, “grisliness." just to pay no heed. Meet different people take different methods to treatment. deliberately finding fault in the" management" are extremely rare, we see in safety management is the most serious criticism, or even fly. In my opinion, as long as the management on subjective intention is not bad, the employee should accept. “Listen to criticism, no cry".
“Strict is the love, the pine is the evil", strictly to the employee from harm to ensure their own good. Employees should understand the strict management starting point. If someone good for him, he will blame on others, it is not to know well from bad, it is quality problem. The management according to the system to do, no matter what the post, no matter what identity, safety before, in front of safety management, safety management system before, makes no exception. Punished, employees have little reason to scold managers To scold system only, and not for each system employees developed a person, called system also makes no sense.
Of course, safety management no cry no cursing, just the ideal realm. No cry "is our pursuit of the results; not condemning, many cases is less likely to. Because, people of different interests, ideas, culture level are different, be punished to reflect different. However we can do in a fair of management, if keep” evenhanded ", people did not have any words. The management of human nature, respect others &respect yourself, let be the managers know that the managers ” intentions, to achieve the
" no voices no cry" safety management ideal situation.
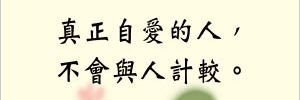

相關範文
- ·關於安全生產的演講稿
- ·做安全生產的熱心人、明白人((安全生
- ·安監局長關於安全生產發言稿
- ·安全生產 國泰民安|2006年全國安
- ·縣安全生產監督管理局2007年安全生
- ·關於2007年糧食生產的意見
- ·鄉鎮黨委政府關於2006年發展烤煙生
- ·關於2005年糧食生產的意見
- ·關於開展“決戰年終90天,實現安全生
- ·關於安全的名言警句
- ·關於安全的句子
- ·關於安全的廣告語
- ·關於安全的徵文精選
- ·關於安全的名言
- ·關於安全的格言
- ·關於安全的一句話
- ·關於安全教育的演講稿
- ·關於安全演講稿
- ·關於安全的徵文
- ·關於安全的國旗下講話
- ·關於安全的演講稿
- ·關於安全方面的演講稿及徵文
- ·關於安全的標語
- ·安全生產月安全徵文
- ·煤礦開展“決戰年終90天,實現安全生
- ·安全生產比賽演講稿:安全之責重於泰山
- ·安全生產及安全社區創建活動方案
- ·我說安全(安全生產月演講稿)
- ·安全伴我同行(電氣部門安全生產月總結
- ·追根溯源抓安全(安全生產演講稿)
- ·安全生產演講稿:你是安全的我就是幸福