豐田生產方式讀後感
手機:M版 分類:讀後感 編輯:小景
豐田生產方式讀後感 標籤:春晚觀后感
豐田生產方式讀後感(一)
--羅志成
羅志成
在公司的組織下,我閱讀了《豐田生產方式》,直到現在我的心還久久不能平靜,我一直在思考,製造業巨頭、汽車行業領頭羊豐田公司能在短短的幾年內,而且還是在日本二戰戰敗,本國人民情緒低落,全球經濟低潮的時候能一鳴驚人,直到60年後的今天能成為世界第一的汽車製造商,沒有完善的管理體系,沒有科學的生產方式是不可能有今天的巨大成就。豐田能獲得巨大有成功及市場價值不是一天兩天能達成的,正如"Rome was not built in a day"一個企業的發展成功必經是千錘百鍊的,那麼我們能做什麼來幫助豐田生產方式在麥格米特企業中的運用呢?
消除浪費
豐田生產方式即TPS,其哲理就是一個目標,兩大支柱,一大基礎,豐田生產的目標很簡單,一個企業的生存發展都需要獲取利潤,當銷售價格不可能再增長的情況下,那麼獲取最大利潤的唯一途徑就是降低成本,提高效率,提升品質降低成本的途徑很多,而最有效的就是消除浪費,在生產加工過程中,浪費無處不在,最典型的浪費為分七大類:等待的浪費、搬運的浪費、不良品的浪費、動作的浪費、加工的浪費、庫存的浪費、製造過多(早)的浪費。然而除了這七大浪費我覺得還有一大浪費是企業不可忽視的,那就是-人才浪費,人才浪費分為兩類,一是由於崗位定義不合理,有能力的人在做一些平庸的事,碌碌無為,得不到成長,浪費人才;另一類是由於公司或者企業內部管理原因,員工沒有歸屬感導致優秀員工離職,這樣的浪費對企業的打擊是致命的,大家都知道企業要培養一個人才是需要兩到三年的時間,一個對企業有付出,有奉獻能發光發熱的員工,必須有一個熟悉公司管理制度、公司運作模式、公司體系,熟悉這些都是需要時間的。現階段我們IT團隊在開發的HR系統將會解決人才培養、培訓的難題,HR系統將建立完善的人才培養,培訓管理機制,盡最大可能的使人盡其才物盡其用,讓公司的高管做能識千里馬的伯樂,給人才一個機會,一個展示平台,讓人才與企業共同發展。
提高效率和品質
提高效率,提高生產品質,這是一個很大的課題,也是企業的生命線,一個企業如果沒有效率,沒有品質,那就等於死亡。提高生產效率就必須合理安排生產計劃,要有計劃地完成各項工作,分清主次,輕重,企業內外部人員協同合作,團結一致,做好交接棒,做到1+1>2,採用激勵機制,最大限度地發揮員工的主觀能動性,目前的績效考核,不能僅僅是考核員工,更要作為員工考核自己,企業自身提高,提高內部核心競爭力的手段。品質是企業存亡的關鍵,提高品質是任何一家企業的奮鬥目標,豐田採用自動化的手段對品質進行管控,把不良品拒之加工門外。目前我們IT團隊在做MES系統,MES系統對生產各個環節進行追蹤管控,焊機MES系統已經上線,能夠做到從物料來料到生產加工以及到出貨,形成整個流程的生產追蹤及品質管控,另外MES系統中有單獨品質模塊,品質模塊建成上線后,能夠讓生產品質提升到一個新的台階,不但能進行品質異常的提前預警,不讓不良品流入到下一站工序,還能將不良品的整個加工過程進行記錄與分析,能夠讓品質技術人員對不良品的形成進行追蹤分析,防止再次發生。
準時化、自動化
豐田生產的兩大支柱:準時化、自動化,這也是減少浪費的核心,準時化講究的按需生產,拉動式生產,以需求為生產的導向,彈性生產,均衡化生產,哪裡需要走向哪裡,當然準時化的生產是以看板作為前提,MES中的電子看板將發揮其作用,讓生產的每個環節一舉一動都呈現在大家眼裡,沒有看板管理,那麼生產的狀況就是一團糟,庫存,來料,生產,品質等就無從掌握,準時化生產就是空談。目前有很多企業為了獲取市場,盲目的生產擴張,導致庫存的堆積如山,這樣出現了一系列的問題,貨品賣不出去,運作資本周轉不過來,就算舊的產品賣出去了,得不到市場的認可,需要拉回工廠進行重工升級,這樣耗費了大量的人力,物力,這就是浪費的根源。公司計劃把前加工作為準時化生產的先驅,按生產需求發料,不讓生產線有獃滯物料,SMT貼片倉庫的建立完成,把原來從倉庫拉料變成直接從車間配料上線,這些都符合豐田生產的管理理念。自動化,顧名思義,通過運用機器、設備等讓機器來取代人的生產方式,豐田生產的自動化不是完全的自動化,其自動化強調了人的因素,所有的自動化都是建立在人之上,是將人的智慧賦予機器,做到人機完美結合。
5W1H
豐田生產方式的基礎是"改善",改善兩個字是每個生產者及生產現場管理者應該銘記於心並且時刻運用到生產中來的,簡單的兩個字卻是生產中最有幫助與啟示的,怎麼樣做好改善,那就需要用到我們充滿智慧的大腦,凡事多用5W去分析,多問5個為什麼,為什麼會這樣,為什麼在這個時間點會出現,為什麼上次沒有發現,為什麼其他人沒有提出,為什麼……只有在自己內心深處多問幾次為什麼,那麼答案自然也就出來。現在的5W已經升級了,變成了5W1H,從為什麼到了怎麼樣解決,經過全盤考慮這六個問題,計劃就不會僅僅停留在一張紙面上而永遠得不到執行。最後改善完成,我們把改善的成果形成一個制度,一個成熟的方案納入到企業的日常管理之中。
當今中國,人口紅利不在,大多數生產製造廠商移至東南亞及其他有人口紅利國家,製造行業的冬天將到,麥格米特想在行業中做到一支獨秀,那麼將要做到開源節流,提高企業內部核心競爭力,學習豐田生產方式是我們現階段必須做的一門功課,只要不斷與學習、反思、總結才能與時俱進,我們的企業才能做大做強,我們的員工才能得到發展,實現雙贏。
最後作為一名在生產一線的管理者,我們一起來讀一讀改善之魂,這也是我從事IE六年來的工作之本,也是立足之本,為麥格米特的明天,我們一起共勉:
改善不要求一改到底,即使只完成了一半也是成功
遇到困難不要以為實現不了,應該想如何才能實現
遇到錯誤,立即糾正
三個臭皮匠頂一個諸葛亮
凡事多問五個為什麼
做不花錢的改善
改善是無止境的
豐田生產方式讀後感(二)
沒有一個國家的企業能像日本豐田那樣帶給全球汽車製造業如此深刻的影響。這種影響源自品牌的塑造和其獨特的商業文化,以及技術創新和極具前瞻性的意識革命。作為一個汽車製造商,它在日本正以驚人的速度和其他廠家無以匹敵的架勢擴大規模,進行併購並以製造出足以統治全球汽車工業的傑出車型為目標。如今,豐田的生產管理取得了巨大成果,銷售業績長期保持增長,儘管在 2008 年,全球經濟蕭條的情況下,它依然能獨佔鰲頭,它的標杆意義已經不再局限於汽車製造業,而是在許多領域成為卓有成效的領先者。
鑒於這個原因,也是作為一名精益從業者的好奇,我懷着崇敬的心情,拜讀了豐田生產方式創始人大野耐一的這本著作。在這本里,我看到,從豐田織布機到今天涵蓋整個汽車產業鏈各個領域的豐田株式會社一步步走來的辛酸歷程。
這本書自出版以來,被很多豐田生產方式愛好者拜讀研究,我也看過很多類似的文章。有人從中看到了豐田佐吉發明自動織機時提出自働化的敏銳觀察力和創造力,更佩服他深入現場精神;有人看到了豐田喜一郎在一個大規模生產成流行的時代提出:準時制的概念——按照規定的時間,配送規定數量的合格品,應該是對一個時代的挑戰和創新,這種精神值得欽佩;但是我看到的是,豐田汽車最困難的時候,上下一心,向著目標一步一個腳印邁進的踏實精神。
二戰後的日本,千瘡百孔,百廢待興,在這樣的環境下,沒有廠房,沒有機器,沒有足夠的人力,但是就是在這樣的環境下,用最少的資源,豐田公司創造了奇迹。沒有廠房,用木板搭個棚子就可以生產,沒有錢買大型機床,那麼就用功能最少的機床實現需要的操作,沒有人力,那麼,我們就自己培訓。看到這裡,你肯定要說,當時的豐田對產品質量太不負責了。不,你錯了,豐田的理念是:有鋼要放到刀刃上。廠房可以破,但是機器不能差,雖然不能買組合機床,但是功能單一的機床的性能卻絲毫不差;沒有員工,那麼就引進美國戰時訓練工人的系統培訓工具: TWI ,對員工展開迅速而有針對性的培訓。就這樣,一套不追求多功能設備的企業,一套擁有自己完整人力資源培養機制的企業,在貧瘠的大地上創造了自己的輝煌。
今天,作為中國人的我們,是否應該覺得汗顏,我們地大物博,我們資源豐富,但是,我們的工業水平卻遠遠落後於日本。
那麼我們如何自強?百年之前,我們的先人就提出了:師夷長技以自強的口號。我想這句話,在現在依然有深遠的意義,我們的工業現階段是落後了,但是我們要知道什麼是先進的,什麼是值得學習的。日本豐田在運營管理方面做的好,我們向他們學習又何妨?我們只要知道自己的目標,學習精華,剔除糟粕,總有一天,我們的民族工業也會有大放光彩的一天!
豐田生產方式讀後感(三)
日本的產品在世界上一直以簡潔小巧、精緻、質量好、功能先進等優點著稱。為了保持產品競爭力的不斷提升,必須降低產品價格,同時保證產品品質保持原有水平,甚至超越原有產品,因此想方設法降低成本、提高科技含量,成為了日本公司重點研究的課題。
對於大批量製造,從流水線上生產出的產品而言,原材料成本和管理成本構成了日本產品的主要成本。由於日本資源有限,產品的原材料大多進口,成本不容易控制,因此如何控制管理成本是決定產品價格能否下降的主要因素。
"即使是乾燥的毛巾,如果動腦筋也能讓它擠出水",這句名言出自豐田汽車工業社長豐田英二。多數企業在談到如何改進管理提高效率時總以人員配備合理、生產效率已經很高等等的理由來表示公司的效率已沒有可以提升的空間。然而用豐田的生產方式來對照企業現有的生產方式仍然能夠發現有許多不足,似乎還有許多" 水分" 可以擰出。
消除浪費是豐田生產方式的唯一目的。消除浪費是降低成本的有效手段。在製造過程成本中,豐田總結了7 種浪費。生產過剩的浪費、製造不良品的浪費、停工等活的浪費、動作上的浪費、搬運的浪費、加工本身的浪費、庫存的浪費。豐田將浪費的定義範圍擴大化,把只使成本增加而不產生附加價值的作業都稱為浪費,以上7 種浪費即是" 干毛巾中的水分" .豐田認為控制並改善這些浪費就能提高效率並且高品質的生產。
豐田生產實現消除浪費的兩大支柱是,及時化與自働化。
及時化是指在需要的時候按照需要的量生產需要的產品供給各工序。多數企業認為機器及員工在8 小時內不停工作,生產商品就是機器利用率以及人工效率最大化了。豐田則認為這樣會生產出很長一段時間銷售不出去的產品,這樣的結果有兩個缺點:1 、流動資金占用率提高了。資金是有成本壓力的,對於其他更有用的投資減少了,效益也就相對下降了;2 、同時庫存增加了,堆放了銷售不出去的產品,佔用了倉庫空間,需要更大的倉庫堆放產品,造成了成本的增加。豐田的及時化有效解決了這兩個問題,通 過生產流程化、按需求數量確定生產節拍、后道工序領取方式及小批量生產的方法,實現靈活對應需求變化、消除生產過剩的浪費、縮短前置時間的目的。
自働化是在機器上安裝了" 能夠判斷機器作業狀況好壞的裝置" ,當發生異常狀況時,傳感器就會感知到異常,自動停止機器設備的運轉。傳統的自動化指當機器產生故障時,只要人不切斷開關就會繼續生產,導致不斷地生產不合格產品。同時由於查找原因的時間滯后,很難把握真正的原因。自働化把重點放在阻止生產線的流動上,自動停止生產,不把不合格產品送往下一道工序。
《實踐豐田生產方式》一書詳細闡述了企業有降低成本空間的六個原因,並通過及時化與自働化兩大支柱進行改善,同時以看板管理、均衡化生產、合理配置設備、標準化作業等輔助方式最終實現消除浪費,創造高質量、高收益的目標,為企業提供了寶貴的經驗,值得我們學習和借鑒。
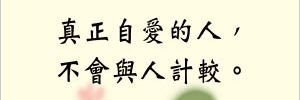

相關範文
- ·讀《豐田生產方式》有感
- ·電網生產方面各項工作思路
- ·安全生產方案
- ·糾正安全生產方面損害群眾利益行為專項
- ·構建教育新模式讀後感
- ·失竊的公式讀後感
- ·會思考的豐田現場讀後感
- ·論依法執政的思維方式和工作方式
- ·豐田招聘:培養企業管理者
- ·豐田精益管理心得體會
- ·《經濟學的思維方式》讀後感
- ·安全生產 國泰民安|2006年全國安
- ·縣安全生產監督管理局2007年安全生
- ·做安全生產的熱心人、明白人((安全生
- ·創新第二批先進性教育學習方式
- ·教學反思:教學方式
- ·寄求職信,別忘了寫明你的聯繫方式
- ·寄求職信,別忘了寫明你的聯繫方式
- ·轉職能轉方式轉作風實施方案
- ·創新工作思維轉變督查方式
- ·《語文教學中對學生學習方式的構建》課
- ·換一種方式計算人生
- ·學習2011版《義務教育數學課程標準
- ·有關愛的文章:愛的不同方式
- ·民事行政檢察監督方式研究要論(2)
- ·用什麼方式看見另外的生命?
- ·看12求職方式哪種成功率高
- ·改進和完善鄉鎮執政方式研究
- ·競聘演講結尾的幾種方式
- ·紀檢監察系統轉職能轉方式轉作風大討論
- ·2005年扶貧到戶貸款貼息方式改革試