讀《豐田生產方式》有感
手機:M版 分類:讀後感 編輯:得得9
讀《豐田生產方式》有感(一)
--王利濤
豐田生產方式,用一句話概括:"不僅僅是一種方式,更是一種追求。
上個世紀的石油危機,和現在的經濟疲軟,一大波一大波的企業都難以度過這樣的寒冬。一個企業的生存法則就是賺錢,盈利。大野耐一先生領導的豐田公司同樣也面對這樣希望渺渺的未來。面對這樣的問題,大野耐一建立了豐田的兩個支柱:準時性(JUSTIN TIME)和自動化。
準時性和自動化帶來了成本的不斷下降以彌補價格上的劣勢。消除成本問題,就是減少各種浪費。雖然豐田生產方式本書描述的是上個世紀的工廠生產方式,但是他其中的精髓仍然是我們現在生產活動的指導方針。排除浪費任何一絲材料、人力、時間、能量、空間、程序、搬運或其他資源。即排除生產現場的各種不正常與不必要的工作或動作,時間,人力的浪費。這個也就是我們常常所說的8大浪費。減少8大浪費就是降低我們的生產成本,這個就是能夠屹立於製造產業的不二法寶。例如公司將SMT物料倉庫搬到SMT生產線旁邊,在很大程度上解決了物料的搬運時間,人力成本,運輸過程中的損耗丟失等。在與8大浪費作鬥爭的時候,5W工具也同時被提出來了。面對每一個浪費的時候,能夠充分運用好5W工具,想必一定能夠事倍功半。減少了浪費,使生產能夠實現準時性,還需要目視管理+看板這樣的現場管理方式。目視管理可以讓管理人員快速的明白,生產現場發生了什麼,以便快速的決策做出相應的行動。同時看板,可以讓生產現場的所有人都能夠明白,我們現在正在做什麼,將要做什麼,讓自己的所有行動能夠有據可依,而不是一臉茫然。良好的看板體系和目視管理,也是減少浪費的一種方式。我們SMT後續將推行目視化管理,所有的機器掛上相對的吊牌,生產線前面用看板展示每小時的產量達成,良率,DT信息等。
不斷的改進生產水平,不斷的提升管理水平,這個是豐田成功的法寶,也是我們成功的法寶。不論是看板,還是生產平衡化,亦或是標準化生產,這些都是豐田能夠成功的方法,但是並不是豐田成功的核心。豐田成功依靠的是人,而不是這些方法。人才是豐田面對石油危機的制勝法寶。面對世界上通用的大量批量生產方式,大野耐一頂住各種壓力,推行小批量快速切換,準時自動的生產方式。這個不僅僅是聰明的管理經營方法,更是一種勇氣的體現,一種責任心的驅使。創始人豐田老先生將豐田公司管理權限交到大野耐一手中,就如同我們得到了上級安排的任務,大野並不是簡單的將這份工作完成而已,而是用了20年的時間,來將這份工作化為自己的使命。因此不管是作為一個車間的領導,還是一個廠的廠長,大野耐一都在每個車間設置一個辦公座位,親自到每個流水線,每一個工作崗位去學習,去研究,去改善。結合三現主義,將自己的理念植入在豐田的每個角落。面對任務,面對挑戰,如果我們每一個人都能夠做到將公司的願景當成自己的願景,將每一件事做到極致,那麼下一個豐田將是麥格米特。
豐田生產方式這本書,給我們帶來的生產理念,已經在世界大部分的工廠之中得到了踐行,但是出彩的工廠寥寥無幾。大部分公司還是需要將精益生產的理念認認真真的傳遞到公司的每一個人,不管他是產線的操作人員,還是公司的上層領導。這樣便能夠建立好豐田生產方式的基礎。更為重要的是,我們每一個人都要有一種危機感,一種責任感,就像龜兔賽跑一樣,需要兔子一樣的速度來進行生產改善,也需要烏龜那樣一步一個腳印,朝着目標永不言棄的前進。
讀《豐田生產方式》有感(二)
--汪林群
讀過《豐田生產方式》這本書後,我感觸最深的是,豐田始終把浪費看做最強的敵人,把提高效率和降本緊密在一塊,不做無用功,只做有價值的產品。這就體現了豐田一絲不苟的務實精神,並為實現精益化生產打下牢固的執行基礎。作為與生產緊密相關的採購執行部門,讀完這本書後還有以下5項有着深刻的體會:
標準化
準時化管理是無浪費管理,即"在正確的時間,正確的地點,保質保量的供應生產所需求的人力、設備、材料等。採購過程中準時化管理可以減少庫存、提升庫存周轉率、提高現金流轉速度,從而讓公司創造更多的價值,更具竟爭力。
1、準時化:根據交貨計劃,將需要的材料、配件在需要的時刻按需要的數量,不多不少地交回指定地點。
2、實際時了解存貨情況,以備把準時化工作做得更為細緻。
認識浪費,杜絕浪費和"需求量"等於生產量
徹底杜絕浪費以提高生產效率,降低成本是企業當前急需面臨和處理的問題,豐田創業初期用最少的資源創造了奇迹,時至今日乃至全球仍沒有幾家企業能像豐田那樣帶給製造業如此深刻的影響。這種影響源自豐田思想和技術的創新以及其對品牌的塑造。儘管在全球經濟蕭條的情況下、在當今企業利潤受到衝擊的情況下它依然能獨佔鰲頭,這與豐田杜絕浪費、"準時化"和"自動化"生產方式是密不可分的,"準時化"和"自動化"是為了杜絕浪費,杜絕浪費最根本的目的就是降低成本,用同樣的成本創造更高的價值,讓企業更有竟爭力,過多、過早製造會造成浪費;不必要的庫存會導致浪費;質量問題會帶來浪費;生產線上等待也會形成浪費;過多的人員、過多的庫存、過多的設備等都會產生驚人的浪費,增加企業的成本。採購執行部針對降低成本也有一些新的理解,後續工作中要學習"看板"管理模式,利用"自動化"與"準時化"兩大支柱來強而有力的杜絕浪費。力求做到"需求量"等於生產量,減少物料等待時間,降低庫存風險, 減少庫存"浪費".改變固有的思維模式,滿足工作的需求,承擔自己的責任,積極創新,學以致用。
1、自動化:了解相關材料、配件的原材料周期、生產周期等,建立系統性資料,利用ERP系統運算,結合實際需求適時給到供應商合理的交貨計劃再進行跟進。
真正的原因"比"原因更重要
如缺料是為什麼?是訂單下單晚?為什麼下單晚?還是其它原因?學習豐田式反覆問5個"為什麼",查明事情的因果關係或者隱藏在背後的真正原因。現我們採購執行部出現最多的還是不常用供應商沒有跟進到位,下單后需要立即電話或郵件提醒查收訂單。現針對這塊已經請IT系統自動設置導出以下數據,通過系統自動導出權限拿數據說話更直觀更有說服力。綜合以下數據來分析原因:
1、下單及時性(每天14:00-15:00導)
2、未交超期(依據APS周一、周四導)
3、廠商發運7天以上是否已進檢
4、:交貨達成率每個月導,交付及品質等無法達成我司要求的廠商約到株洲來溝通協商處理
目視化管理和信息系統
"目視化管理"是通過"自動化"就能實施。也能杜絕現場中多生產的無效勞動,防止生產不合格品的產生,也能讓企業更好的解決生產中的難題。
目視管理也是利用形象直觀而又色彩適宜的各種視覺感知信息來組織生產現場達到提升效率的一種管理手段,後續採購執行部要多走出去,去供應商現場了解工藝、材料渠道、技術、管理等,綜合這些才能更有效的掌握了解廠商瓶頸,有句話說得很好,沒有了解調查沒有發言權。
貫徹標準作業
1、供應流:客戶-→市場→計劃→採購(執行部)→供應商
2、付款流:財務→採購(執行部)→供應商
3、 需求期目標85%以上, 承諾期目標90%以上, 配合認證降低成本及配合相關兄弟部門推動流程及作業規範。
7月15號被動件執行採購晏艷純在供應平台只有獨家的情況下,利用自已原有的資源找到了現貨,並在滿足交付的前提下直接節省成本RMB12000元,做為採購就是要溝通、思考、討論、總結 …
通過對《豐田生產方式》這本書的學習,不單生產可以通過自動化來提升品質效率,採購同樣也可以通過系統來提升時效率,豐田汽車最困難的時候,上下一心,向著目標一步一個腳印邁進創造了今天的輝煌,我們做為麥格米特團隊的一員,要學習豐田人上下一心,團結奮進,勇於創新的精神,圍繞公司的目標、共同努力,共同學習,認識浪費,杜絕浪費,創造屬於麥格米特的未來。
讀《豐田生產方式》有感(三)
--吳小雁
通過對《豐田生產方式》這本書的學習,使我受益匪淺。豐田生產方式即是一種思想體系,又是一種理念,更是一種文化。豐田人始終把浪費看作是最大的敵人,把生產當成是一種永無止境的精益求精的過程。作為跟生產密切相關的計劃部門,看完這本書後除了對浪費感觸最深外還對以下幾點有着深刻的認識:
強調實時存貨(Just In Time)(可理解為在線庫存)
依據顧客需求,生產必要的東西,而在必要的時候,生產必要的量,這種豐田獨創的生產管理概念。
從豐田生產方式中的看到實時存貨,想到我們目前的現狀車間產品堆積太多,成品、半成品、原材料到處都是,主要造成原因,成品、半成品生產不配套,在線庫存產線管理零亂,產能分佈不均衡,物料異常問題多,交貨緊急換線頻繁 ,結合豐田生產方式中強調的實時存貨,計劃方面措施:成品與半成品配套工單生產,按標準產能合理髮放生產工單數量(半成品、成品),緊急出貨產品按最小物料齊套情況分批發料(MES有現成功能),專用半成品備料正常入庫倉庫統一管理。
標準作業徹底化(周期時間、標準存量)
對生產每個活動、內容、順序、時間控制和結果等所有工作細節都制定了嚴格的規範。但這並不是說標準是一成不變的,只要工作人員發現更好更有效率的方法,就可以變更標準作業,目的在於促進生產效率
俗話說:無規矩不成方圓,規矩的就制度,(范_文_先_生_網)就是從標準化作業中進化而來的,標準化作業不單是生產的標準化作業,也適用計劃,前期由於計劃人員不夠、技能不熟練,大家走了一些捷徑,沒有按流程走,在工作中造成了一些不必要的困擾,比如:物料需求隨意修改,造成多買或是少買物料,物料不良退換料單據未及時(完工工單關閉不及時)等,現在計劃人員基本配齊,工作技能越來越熟練,要改掉這些不良的習慣,要按統一要求來操作,標準化操作迫在眉睫,標準化操作程序文件已疏理,PMC和MC程序文件已寫完,待討論后按統一標準來操作。
生產平衡化(投入/產出平衡)
豐田所謂平衡化指的是"取量均值性".豐田要求各生產工程取量儘可能達到平均值,也就是前後一致,為的是將需求與供應達成平衡,降低庫存與生產浪費
生產平衡化與實時庫存是相輔相承的,生產不平衡實時庫存肯定高。生產平衡需要多個部門的共同努力才能達成,不是一個單方面的努力就有效果的,計劃平衡是生產平衡的基礎,計劃平衡是建立在各方資源信息共享的基礎上的,即計劃在安排計劃時需要了解各方面信息(市場、物料、產能等),市場信息是依據,物料是前提,這樣才能計劃平衡、生產平衡,用MES來編碼看板式生產計劃。
團隊作業與交接棒(可理解為責任心)
團隊作業高於一切,互助運動是保持強有力團隊協作生產的動力,接力棒交接提如何是團隊取得好成績的關鍵,準時化是團隊間相互配合的協作精神,自動化則是提高每個隊員的個人技術。
剛剛過去的籃球比賽,採購計劃部憑藉團隊協作精神和個人技能,在沒有備用人員的情況下衝出困境贏得比賽,這就是團隊作業的結果。
自動化
充分發揮人在流水線當中的作用,改變機床或其他生產設備的排列方式,用最少的人管理最多的機器,改變以往定員制的機器管理方式,提高每個人在生產中的工作效率,真正做到"省人化"而不是利用各式先進的機器達成的"省力化".
通過對《豐田生產方式》這本書的學習,不單生產可以通過自動化來提交品質效率,計劃也可以通過IT手段來提高效率,通過MES制訂計劃看板能更直觀有效的實現計劃的信息共享,通過IT和MES手段,使計劃效率更快更高效,公司各部門時時了解各產品計劃狀態;計劃部根據市場預測及訂貨而制定生產指令下達生產部,各道前工序的生產都根據看板來進行,這相當於生產工作指令單。使用看板可以促進工作改善,防止過量生產與過量運送,對生產現場進行目視管理。了解看板管理后,目前公司運行的是ERP系統及現在正在上MES系統都是建立在看板管理的基礎上的,每一道工序間進行聯網,指令的下達、工序間的信息溝通都通過ERP和MES系統來完成。而看板方式更具實用性,它能讓生產線上的相關人員參與進來,適量生產,防止過量生產引起新的浪費。
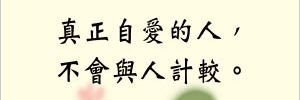

相關範文
- ·豐田生產方式讀後感
- ·《經濟學的思維方式》讀後感
- ·觀《紀念中國人民抗日戰爭暨世界反法西
- ·電網生產方面各項工作思路
- ·安全生產方案
- ·糾正安全生產方面損害群眾利益行為專項
- ·論依法執政的思維方式和工作方式
- ·豐田招聘:培養企業管理者
- ·《函數•方程•
- ·會思考的豐田現場讀後感
- ·《劉強東自述:我的經營模式》讀後感
- ·豐田精益管理心得體會
- ·《豐碑》教學反思
- ·莫言的《豐乳肥臀》讀後感
- ·《豐乳肥臀》讀後感
- ·《豐乳肥臀》讀後感
- ·《豐盈的心》
- ·正面管教《換種方式做父母》有感
- ·讀《高員工流失率下的精益生產》有感
- ·讀《教出樂觀的孩子有感》有感
- ·讀《三國演義有感》有感500字
- ·安全生產 國泰民安|2006年全國安
- ·縣安全生產監督管理局2007年安全生
- ·做安全生產的熱心人、明白人((安全生
- ·讀《水滸傳》有感650字
- ·讀《正能量》有感
- ·讀《夏洛的網》有感
- ·讀《湯姆叔叔的小屋》有感500字
- ·讀《朝花夕拾》有感800字
- ·讀《致加西亞的信》有感1500字
- ·寒假讀後感——傾聽心靈的歌聲讀《狼王